The Future of Welding: How Innovation and Sustainability are Reshaping the Industry
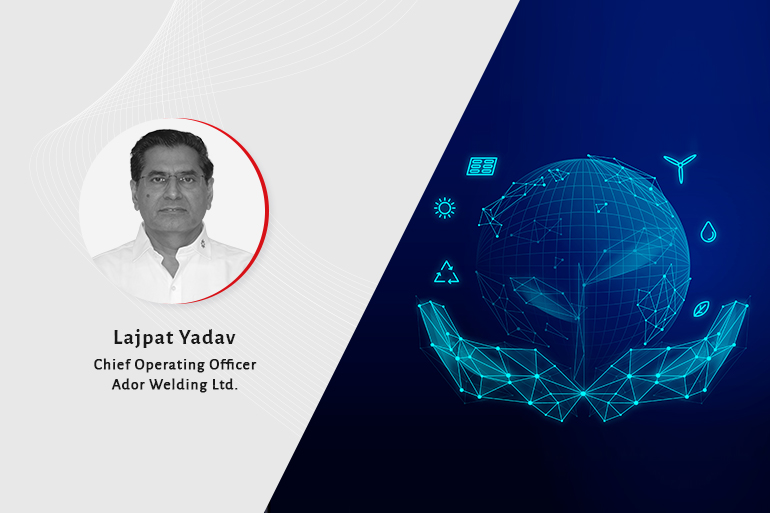
Smart Technologies and Eco-Friendly Practices are Paving the Way for Efficiency, Sustainability and Next-Generation Problem-Solvers
Introduction
The welding industry has long been the backbone of key sectors such as shipbuilding, power and energy, automotive, manufacturing, infrastructure, and military defence. While welding techniques have evolved to keep pace with technological advancements, sustainability has emerged as a new priority.
Industries worldwide are moving toward green welding practices that reduce environmental impact while improving operational efficiency. Breakthroughs in renewable energy, waste management, and resource conservation are now merging sustainable solutions into welding to build a more responsible and future-ready industry. The welding sector is significantly transforming, prioritising energy-efficient solutions, water conservation, green packaging, optimised logistics, and workforce training. These factors collectively contribute to reducing carbon footprints while maintaining productivity and performance.
Smarter Energy Use in Welding
Historically, welding has relied on diesel generators and conventional power sources, leading to high fuel consumption and emissions. However, modern technologies are enabling industries to reduce energy usage while retaining the same level of performance.
Key Energy-Efficient Innovations
- Battery-Powered Welding Machines: Portable and rechargeable solutions eliminate reliance on fuel-powered generators, reducing emissions and operational costs while providing mobility for remote projects.
- Solar-Powered Systems: The integration of renewable energy into industrial operations allows solar-powered welders to decrease dependence on fossil fuels while lowering greenhouse gas emissions.
- Inverter-Based Welding Machines: These machines adjust power output based on demand, consuming less energy than traditional alternatives, preventing energy wastage and improving efficiency.
Conserving Water in Welding Processes
Whether for cooling machinery or maintaining operations, water plays a crucial role in welding. However, traditional welding processes tend to overuse water, leading to waste. Sustainable welding techniques minimise water consumption through innovative solutions.
Water-Saving Techniques
- Closed-Loop Cooling Systems: These systems reuse water multiple times a day, significantly reducing waste
- Rainwater Harvesting: Collected rainwater can be used in cooling towers and certain welding equipment, lowering freshwater dependence.
- Advanced Plasma Cutting Technology: New plasma welding and cutting techniques require less water than traditional models, contributing to conservation.
Sustainability in Packaging
The transportation of welding materials across long distances underscores the importance of durable and eco-friendly packaging. The industry is shifting towards more sustainable packaging materials that reduce waste and environmental harm.
Key Trends in Green Packaging
- Recyclable and Biodegradable Materials: Moving from plastic-based consumables to paper-based, compostable, and biodegradable alternatives reduces environmental impact.
- Reusable and Returnable Containers: Durable packaging solutions help minimise waste while increasing longevity.
- Lightweight Packaging Designs: Compact designs lower transportation emissions while reducing overall shipment weight.
Optimising Transportation and Logistics for Efficiency
Beyond packaging, optimising transportation and logistics is critical for reducing the carbon footprint of the welding industry. Companies are now adopting smart strategies to improve efficiency and sustainability.
Sustainable Transportation Solutions
- Compact Packing Methods: Efficient packaging allows more units to be shipped per trip, reducing fuel consumption.
- AI-Driven Route Optimisation: Logistics systems analyse and determine optimal delivery routes, cutting unnecessary travel and emissions.
- Sourcing Lightweight Materials: Using lightweight materials for packaging decreases shipment weight, lowering fuel consumption and environmental impact.
Upskilling the Workforce for a Sustainable Future
While technology drives transformation, skilled professionals remain the force behind sustainable welding. Training the workforce is essential to ensure the successful adoption of green advancements in the industry.
Key Areas for Training
- Energy-Efficient Welding Techniques: Teaching eco-friendly welding methods that minimise energy use and reduce material waste.
- Integration of Automation & AI: Regular training on smart welding machines improves precision, efficiency, and sustainability.
- Environmental Impact Awareness: Professionals are educated on tracking and reducing carbon footprints, embedding sustainability in every project.
Conclusion
The welding industry is embracing a future shaped by sustainability and innovation. By adopting energy-efficient technologies, resource conservation practices, and workforce training, welding businesses are positioning themselves for long-term success while reducing environmental impact.
With advancements in automation, AI, and green welding techniques, the industry is set to pave the way for next-generation problem-solvers who will shape a sustainable future. As organisations prioritise environmentally friendly solutions, welding will remain integral to industrial progress, with a responsible approach toward sustainability.